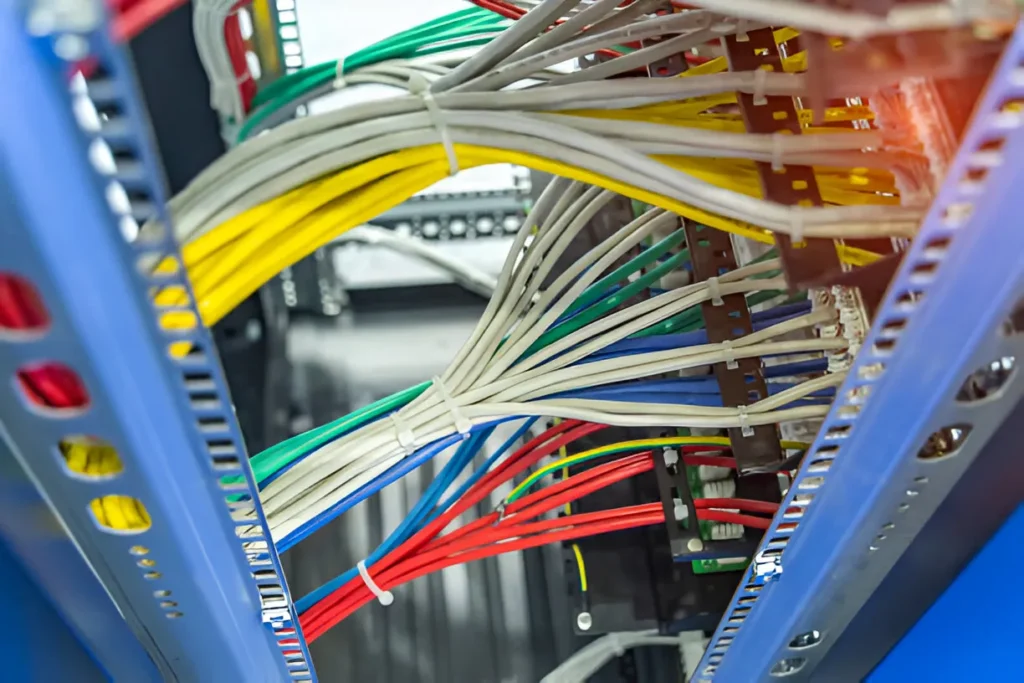
How Cable Ties Are Made
Have you ever wondered how cable ties are made? Cable ties, also known as zip ties, are essential tools for organizing and securing wires and cables.
From raw material selection to the final packaging, the manufacturing process of cable ties involves several intricate steps. In this blog post, we’ll explore the fascinating journey behind the creation of these humble yet indispensable fasteners.
What are cable ties?
Cable ties are versatile fastening devices used to bundle and organize cables or wires. They are typically made from nylon, a durable and flexible material known for its resistance to wear and environmental factors.
The design of cable ties includes a ratchet mechanism that allows the strap to be tightened around a bundle of cables, securing them in place. This mechanism prevents the tie from loosening, ensuring that cables remain organized and tidy.
Nylon cable ties
Nylon cable ties are a multifunctional fastener made of nylon material. They have excellent properties such as high strength, high temperature resistance, and wear resistance. There are many types to meet different usage requirements.
They are widely used in electronics, mechanical manufacturing, aerospace and other fields to fix and organize cables, oil pipes, wire harnesses and other items.
Stainless steel cable ties
Stainless steel cable ties are high-performance metal fasteners made of 304 or 316 grade stainless steel, with excellent properties such as high strength, corrosion resistance, and high temperature resistance.
There are various types, including self-locking, prefabricated, and coated types, to meet different usage requirements.
Widely used in industries such as industry, construction, and electricity to fix pipes, cables, and heavy equipment, they have a longer service life and greater reliability than nylon cable ties in harsh environments.

What material is used for cable ties?
Nylon serves as the primary material for cable ties due to its exceptional properties. This synthetic polymer offers high tensile strength, flexibility, and resistance to environmental factors. Manufacturers typically use nylon 6/6, a specific type known for its durability and heat resistance.
The production process begins with nylon pellets, which are melted and injected into molds. This injection molding technique allows for precise shaping of the cable tie’s components, including the flexible strap and locking mechanism.
Some specialized cable ties incorporate additional materials for enhanced performance. Stainless steel cable ties provide increased strength and heat resistance. UV-resistant additives are sometimes included in the nylon mixture to improve outdoor durability.
Manufacturers may also produce cable ties using alternative materials like polypropylene or special blends for specific applications. These variations cater to unique requirements in industries such as aerospace, automotive, and marine environments.
The Comprehensive Manufacturing Process
Raw Material Selection
Manufacturers carefully select high-quality nylon pellets as the primary raw material for cable ties. These pellets undergo rigorous quality checks to ensure consistency and purity.
The specific type of nylon, often nylon 6/6, is chosen for its superior strength, flexibility, and resistance to environmental factors. Additives may be incorporated to enhance UV resistance or other properties based on the intended application of the cable ties.
Melting and Molding
The nylon pellets are fed into an injection molding machine where they are heated to their melting point. The molten nylon is then injected under high pressure into precision-engineered molds.
These molds shape the material into the distinctive cable tie form, complete with a flexible strap, teeth, and a locking head. The injection process ensures uniform distribution of the material and precise replication of the mold’s intricate details.
Cooling
After injection, the molded cable ties undergo a controlled cooling process. This stage is crucial for maintaining the structural integrity and desired properties of the ties. Cooling time and temperature are carefully regulated to prevent warping or other defects. The solidified cable ties are then ejected from the molds, ready for the next stage of production.
Trimming and Inspecting
Once cooled, the cable ties go through a trimming process to remove any excess material or imperfections. Automated machinery precisely cuts away any flash or sprues left from the molding process. Each cable tie then undergoes a thorough inspection.
Quality control measures include visual checks and strength tests to ensure each tie meets specified standards for tensile strength, flexibility, and overall quality.
Packaging
The final step involves packaging the approved cable ties. Automated systems count and bundle the ties into predetermined quantities. These bundles are then packaged into bags, boxes, or other containers suitable for shipping and retail distribution.
Labels and barcodes are applied to the packaging, providing product information and facilitating inventory management. The packaged cable ties are then prepared for shipment to distributors or end-users.
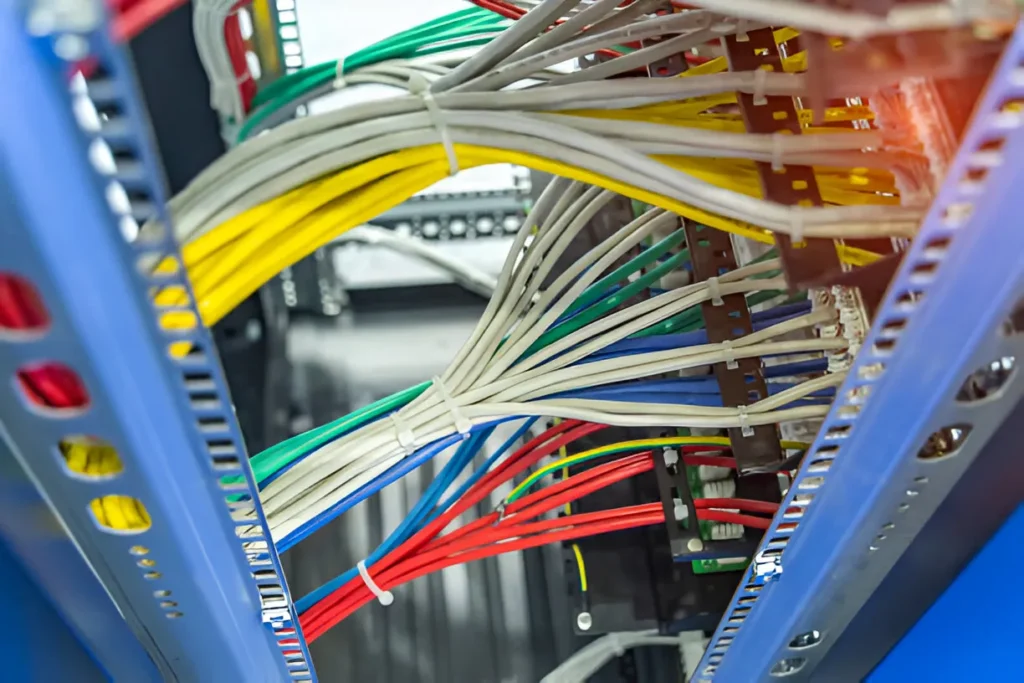
FAQs
1.How are cable ties shaped?
Cable ties are shaped through injection molding, where molten nylon is injected into precision-engineered molds under high pressure.
2.Can cable ties be made in different colors?
Yes, manufacturers can add colorants to the nylon mixture to produce cable ties in various colors.
3.Are there eco-friendly options for cable ties?
Some manufacturers produce biodegradable or reusable cable ties as more environmentally friendly alternatives.
4.How do manufacturers ensure consistent quality?
Quality is maintained through careful raw material selection, precise molding processes, and rigorous inspection procedures.
Conclusion
The manufacturing process of cable ties showcases the ingenuity and precision involved in creating these essential fastening tools. From raw material selection to packaging, each step contributes to the production of high-quality, reliable cable ties.
Next time you reach for a cable tie, take a moment to appreciate the intricate process behind its creation. Explore the various sizes, colors, and materials available to find the perfect cable tie for your needs.